The Challenge of Designing Skid Variants
Automating skid design can significantly reduce the time spent creating multiple variations, making the process more efficient. Skids may not be the most complex component to design, yet when each variation requires a new model and drawing, the time investment quickly adds up. Whether you’re accommodating different motor power ratings or adjusting size constraints and fixing points, the constant need to re-model or modify existing designs can become a significant bottleneck. By leveraging automation, engineers can streamline this process and improve overall productivity.
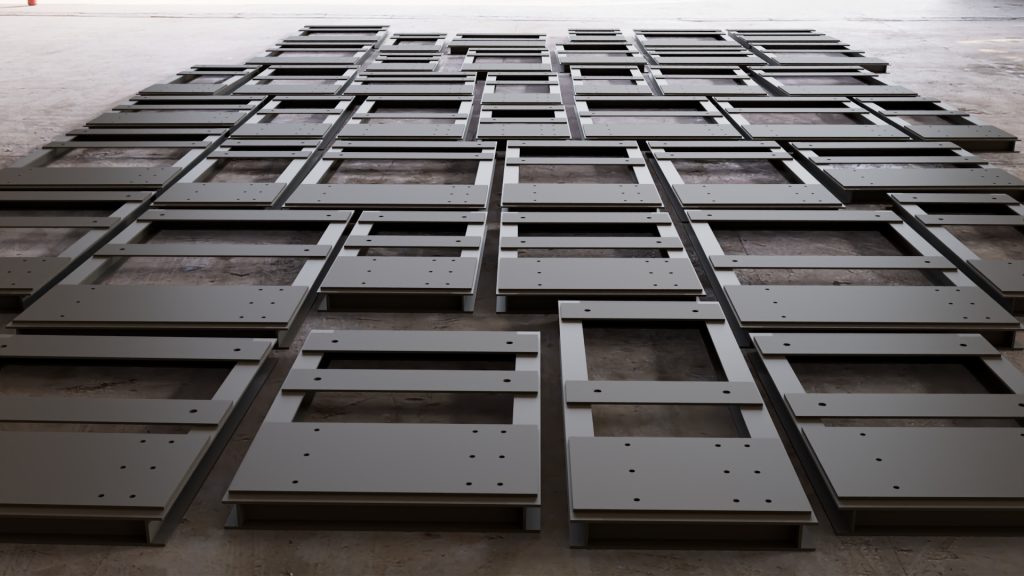
Traditionally, engineering teams have relied on manual adjustments or copying and modifying existing designs to fit new specifications. While this approach may work for smaller-scale projects, it quickly becomes inefficient when dealing with multiple variants. Fortunately, modern CAD tools offer solutions that significantly reduce the time and effort required to create these variations.
The Power of Parametric Modelling
Parametric modelling allows engineers to create dynamic, adaptable designs where key dimensions and features are controlled through variables rather than being fixed. This means that instead of redrawing or modifying each skid manually, designers can input new parameters, and the model updates automatically.
For instance, if a motor’s power rating changes, parametric modelling ensures that the overall skid size, mounting points, and structural supports adjust accordingly without requiring manual intervention. This level of adaptability enhances design efficiency and reduces the risk of errors, especially in large-scale manufacturing or projects requiring frequent modifications.
Key Benefits of Parametric Modelling:
- Time Efficiency – Modify a few parameters instead of redrawing entire models.
- Error Reduction – Minimise the chances of misalignment or incorrect sizing.
- Design Consistency – Maintain uniformity across multiple skid designs.
- Future-Proofing – Easily update designs when new specifications arise.
If you want to learn more about parametric modeling then check out Autodesk’s tutorials here https://www.autodesk.com/learn/ondemand/curated/inventor-parametric-modeling.
Enhancing Skid Automation with Autodesk Inventor’s iLogic
While parametric modelling is a powerful tool on its own, integrating it with automation features such as Autodesk Inventor’s iLogic takes efficiency to the next level. iLogic enables users to embed custom rules and logic-based automations within CAD models, allowing for instant modifications based on predefined conditions.
Using iLogic, you can automate:
- Component Selection – Automatically swap out motors, brackets, or other parts based on performance specifications.
- Size Adjustments – Modify dimensions based on user inputs without needing to manually tweak features.
- Drawing Updates – Ensure that 2D documentation reflects any design changes in real-time.
- Error Checking – Prevent conflicting configurations by setting logical constraints.
This approach drastically reduces the time required to generate multiple design iterations, making it possible to create hundreds of skid variants in seconds. Through API tools such as iLogic even the drawings can be automated form parametric parts as show here https://transientgeometry.co.uk/automating-dimension-placement-in-inventor-drawings/.
A Practical Example: Skid Design Automation
Imagine a scenario where a manufacturer needs to design skids for various motor sizes. Instead of manually creating a new model for each variation, a parametric model with iLogic can automate the process:
- User Inputs Data – The user selects the desired motor power rating and mounting specifications.
- Automated Adjustments – The CAD model updates to reflect the required dimensions, ensuring all fixing points align correctly.
- Instant Variant Generation – Multiple design variations can be produced in seconds.
- Updated Drawings – The associated 2D drawings and documentation update automatically, ready for manufacturing.
By leveraging this workflow, companies can dramatically reduce lead times and free up valuable engineering resources for more complex design challenges.
How Transient Geometry Can Help
At Transient Geometry, we specialise in automation-driven CAD solutions that enhance efficiency and precision in engineering design. Our expertise in parametric modelling and iLogic scripting allows businesses to streamline their workflows, reducing manual effort and improving design turnaround times.
Why Work with Us?
- Custom Automation Solutions – Tailored to your specific design requirements.
- Industry Expertise – Deep knowledge of CAD automation techniques.
- Time & Cost Savings – Minimise repetitive work and focus on innovation.
- Seamless Integration – Implement automation within your existing CAD environment.
Get Started with Automated Skid Design
If your team frequently works with repetitive design modifications, it’s time to embrace automation. By implementing parametric modelling and iLogic-driven workflows, you can save time, reduce errors, and enhance design consistency across all skid variants.
Contact us today to discuss how we can help automate your design process and optimise your engineering efficiency.
Leave a Reply